Di seguito vengono illustrati i componenti di un certificato di calibrazione per gli strumenti di misura della forza.
A seconda del misuratore di forza e della direzione di calibrazione, il contenuto del certificato di calibrazione può variare.
È inoltre possibile scaricare il Certificato di calibrazione del campione Certificato di calibrazione DAkkS del misuratore di forza DKD-R 3-3 (tedesco/inglese).
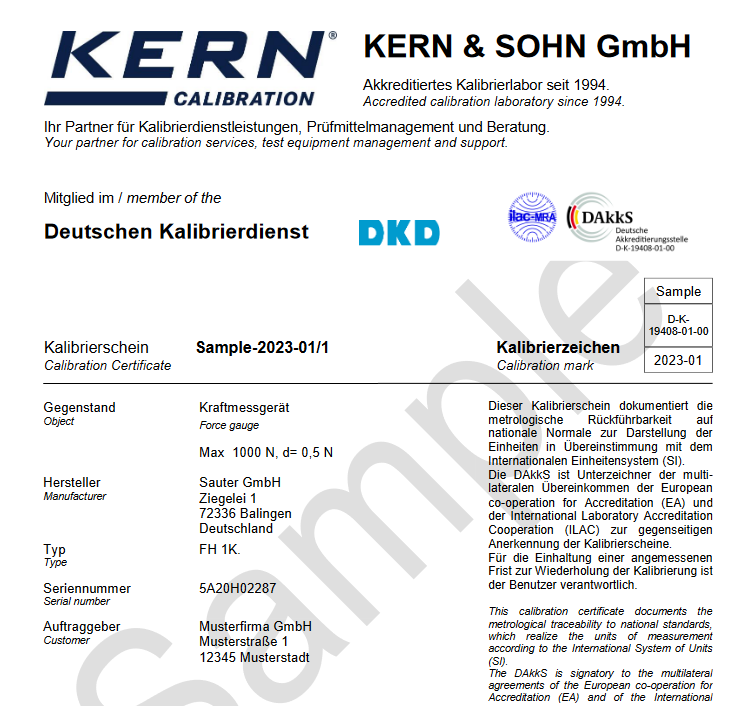
1. Documento "ufficiale"
Il laboratorio di calibrazione DAkkS KERN (D-K-19408-01-00) è accreditato dalla Deutsche Akkreditierungsstelle GmbH. Il certificato di calibrazione DAkkS è riconosciuto a livello internazionale e disponibile in molte lingue.
2. Oggetto di calibrazione
L'oggetto di calibrazione e il tipo o il modello con il numero di serie sono documentati. Questo rende impossibile la confusione e garantisce che il certificato di calibrazione DAkkS sia assegnato a un dispositivo di misurazione della forza esplicito.
3. Tracciabilità
Gli standard di riferimento del laboratorio accreditato sono monitorati in cicli rigorosamente definiti e adeguati periodicamente allo standard nazionale e quindi a quello internazionale. Ciò viene accuratamente documentato in conformità alle normative e indicato sul certificato di calibrazione DAkkS. In questo modo si garantisce l'importantissima tracciabilità allo standard nazionale.
4. Cliente
Sulla prima pagina del certificato di calibrazione DAkkS è chiaramente indicato il cliente o l'operatore dell'apparecchiatura di prova calibrata.
5. Timbro e firma
Secondo la norma DIN EN ISO 17025, è richiesto solo il nome della persona responsabile del rilascio del rapporto. A causa del valore, stampiamo anche il timbro del laboratorio e il nome e la firma della direzione del laboratorio e della persona responsabile del rilascio del referto.
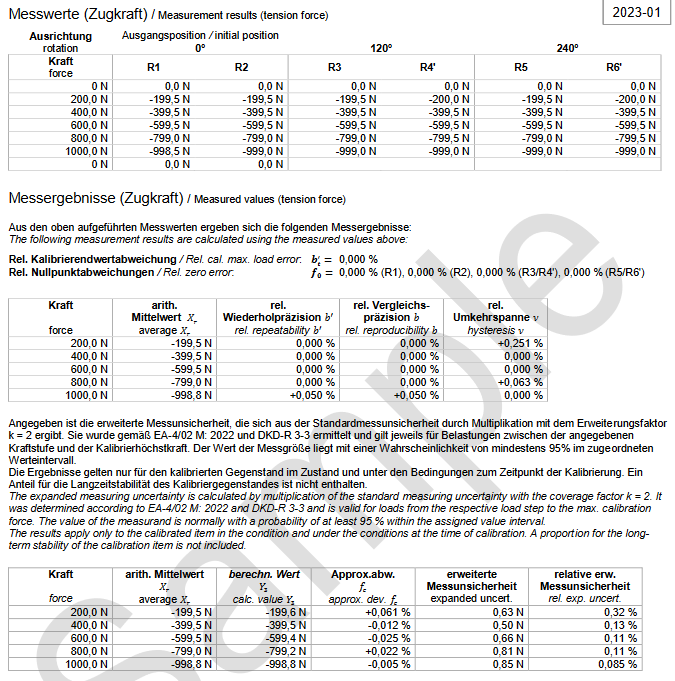
6. Valori misurati
Per ogni direzione di forza, i valori misurati "grezzi" registrati durante la calibrazione sono documentati in questa parte del certificato di calibrazione per la tracciabilità. A seconda delle conoscenze pregresse dello strumento di misura o del suo tipo e, naturalmente, dei desideri del cliente, è possibile utilizzare le varie procedure di calibrazione descritte nella DKD-R 3-3. Le procedure di calibrazione si differenziano per il numero e il tipo di serie di misure effettuate (in particolare le posizioni di installazione e il carico ascendente o discendente) e consentono quindi di adattare lo sforzo di calibrazione alle esigenze di precisione del cliente.
La procedura di calibrazione A è illustrata nell'esempio. Il misuratore di forza viene prima sottoposto tre volte a un precarico con la forza massima di calibrazione. Quindi vengono effettuate 6 serie di misurazioni in 3 diverse posizioni di installazione:
- Carico doppio con carico crescente (serie di misure R1, R2') in posizione di installazione 0° (orientamento solitamente non definito ulteriormente)
- Rotazione dell'unità (fino a 120°), precarico, carico con carico crescente e decrescente (serie di misurazioni R3, R4')
- Rotazione dell'unità (fino a 240°), precarico, carico con carico crescente e decrescente (serie di misurazioni R5, R6')
La ripetibilità può essere determinata caricando due volte in condizioni il più possibile identiche.
La rotazione - e la conseguente necessità di reinstallare il misuratore di forza nel dispositivo di carico - consente di trarre conclusioni sulle imprecisioni specifiche del progetto o del dispositivo nell'introduzione della forza di calibrazione del dispositivo e sulla sua sensibilità ad essa (riproducibilità).
Gli effetti dell'isteresi nel sistema di misura sul valore misurato visualizzato possono essere osservati diminuendo il carico nelle serie di misura R4' e R6'. Il carico meccanico (flessione, torsione) e lo scorrimento dovuto, ad esempio, agli effetti termici fanno sì che il valore misurato differisca dal valore misurato sotto carico quando il carico viene rimosso, nonostante la stessa forza di calibrazione (intervallo di inversione). In particolare, il ritorno a zero è una misura dello scorrimento del dispositivo di misura durante il carico.
7. Risultati della misurazione
I parametri metrologici rilevanti del misuratore di forza calibrato possono essere calcolati dai valori di misura "grezzi". I valori stampati in questa sezione del certificato di taratura sono spiegati qui di seguito; il calcolo stesso è descritto in dettaglio nella linea guida per la taratura DKD-R 3-3.
- Media aritmetica: Il valore medio dei valori di visualizzazione corretti per la visualizzazione dello zero a un livello di carico in tutte le serie di misura. È la migliore stima della lettura del calibro alla particolare forza applicata.
- Ripetibilità relativa b': Misurare la dispersione dei valori di visualizzazione in condizioni identiche.
- Riproducibilità relativa b: Misura della dispersione dei valori di visualizzazione in diverse posizioni di installazione.
- Margine di inversione relativo v: Misura dell'isteresi (e della deriva) dei valori di visualizzazione al diminuire del carico.
- Deviazione relativa del valore finale di calibrazione:
Confronto del display a carico immediato (al precarico) e a carico "lento" con la forza massima di calibrazione (nella serie di misure R1). - Deviazioni relative del punto zero: Confronto del display prima del carico e dopo lo scarico completo, misura della deriva durante il carico
- Y3: Valore di visualizzazione approssimato da un polinomio di terzo grado al rispettivo livello di forza.
- Deviazione approssimativa fc: La deviazione relativa di questa approssimazione dal valore effettivo del display.
- Incertezza ampliata: L'incertezza di misura estesa della deviazione rilevata.
- incertezza relativa estesa della misura: L'incertezza estesa della misura rispetto alla forza applicata.
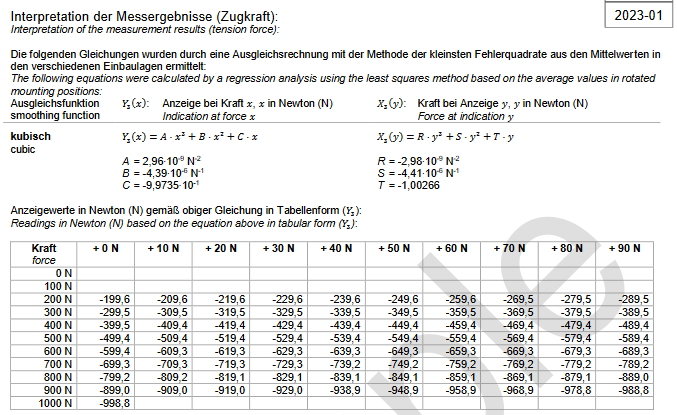
Interpretazione dei risultati di misura
I valori e i risultati di misura riportati nella pagina precedente documentano l'errore di indicazione dello strumento di misura alla rispettiva forza di calibrazione applicata. Non viene fatta alcuna dichiarazione sull'intero campo di misura.
Un calcolo di compensazione che utilizza i valori medi del display nelle varie posizioni di installazione consente di stimare l'errore di indicazione dell'unità in presenza di qualsiasi carico sull'intero campo di misura. Il risultato di questo calcolo di bilanciamento (con un polinomio di terzo grado utilizzando il cosiddetto metodo dei "minimi quadrati") è visibile a pagina 4 del certificato di calibrazione:
- Indicazione Y in corrispondenza della forza x (Y3):
Se viene applicata la forza x, il misuratore di forza deve indicare Y3(x).
La tabella mostra questi valori teorici di indicazione per una serie di forze applicate.
A, B e C sono i coefficienti del polinomio. - Indicazione X in corrispondenza della forza y (X3):
Se il misuratore di forza indica il valore y, la forza effettiva applicata deve essere X3(y).
R, S e T sono i coefficienti del polinomio.